ADELPHI, Md. - Army researchers contributed to the development of lighter armored vehicles for Soldiers with new computational and theoretical models.
According to Army researcher Dr. Benjamin Szajewski, the objective of this research is to improve understanding of the strengthening mechanisms in metal alloys.
Alloys are used in the formation of Soldier and vehicle applications. By improving material strength, less material is required to withstand a given load. In structural applications, less material equates to lighter weight.
The journal Modelling and Simulation in Materials Science and Engineering recently featured this research.
In engineering alloys, microscopic defects created in the alloying process contribute to material strength, Szajewski said. On the microscopic level, material failure occurs through the collective motion of crystalline line defects known as dislocations. At the same microscopic level, on the other hand, obstacles act to block the motion of dislocations. Under stress and loading, the competition between these two mechanisms (dislocation glide and dislocation-obstacle interactions) sets the material yield strength. By preventing dislocation motion, obstacles increase material strength.
“Dislocation-obstacle interactions are an effective strengthening mechanism in metallic alloys,” Szajewski said. “Due to this desirable characteristic, dislocation-obstacle interactions have been a focal point of study for decades.”
Previous efforts, as a whole, are not unified and do not extrapolate well beyond the scope of their individual study.
In this research effort, Szajewski and team have pursued an enhanced quantitative understanding of relationships between physical features of obstacles (e.g., size, shape, elastic mismatch) and strengthening within metallic alloy systems.
The scope of this research has included computer simulations and theoretical modeling efforts, he said. The computer simulations have been conducted using a multiscale simulation methodology, much of which has been developed at the U.S. Army Combat Capabilities Development Command, known as DEVCOM, Army Research Laboratory. The theoretical modeling efforts are built upon the researchers’ understanding of mechanics and statistics of materials.
“The outcome of these efforts is an improved understanding of strengthening mechanisms in metal alloys,” Szajewski said. “The main results relate alloy strength to collective interactions between microscopic crystalline defects known as dislocations and additional obstacle-type defects. The physical modeling conducted in these works does not rely on fitting parameters and moreover is based on an understanding of the underlying physical process. In addition, the developed physical models unify many of the results presented in earlier works found in the literature.”
The significance of this research comes down to three unique outcomes:
“I am optimistic that the results of this research will contribute to our scientific understanding of this strengthening mechanism in metallic alloys,” Szajewski said. “Since metallic alloys have a long–standing role in numerous engineering applications, including armor, improving our understanding of material strength may lead to improved metallic alloy development for various Soldier and vehicle applications.”
www.army.mil
According to Army researcher Dr. Benjamin Szajewski, the objective of this research is to improve understanding of the strengthening mechanisms in metal alloys.
Alloys are used in the formation of Soldier and vehicle applications. By improving material strength, less material is required to withstand a given load. In structural applications, less material equates to lighter weight.
The journal Modelling and Simulation in Materials Science and Engineering recently featured this research.
In engineering alloys, microscopic defects created in the alloying process contribute to material strength, Szajewski said. On the microscopic level, material failure occurs through the collective motion of crystalline line defects known as dislocations. At the same microscopic level, on the other hand, obstacles act to block the motion of dislocations. Under stress and loading, the competition between these two mechanisms (dislocation glide and dislocation-obstacle interactions) sets the material yield strength. By preventing dislocation motion, obstacles increase material strength.
“Dislocation-obstacle interactions are an effective strengthening mechanism in metallic alloys,” Szajewski said. “Due to this desirable characteristic, dislocation-obstacle interactions have been a focal point of study for decades.”
Previous efforts, as a whole, are not unified and do not extrapolate well beyond the scope of their individual study.
In this research effort, Szajewski and team have pursued an enhanced quantitative understanding of relationships between physical features of obstacles (e.g., size, shape, elastic mismatch) and strengthening within metallic alloy systems.
The scope of this research has included computer simulations and theoretical modeling efforts, he said. The computer simulations have been conducted using a multiscale simulation methodology, much of which has been developed at the U.S. Army Combat Capabilities Development Command, known as DEVCOM, Army Research Laboratory. The theoretical modeling efforts are built upon the researchers’ understanding of mechanics and statistics of materials.
“The outcome of these efforts is an improved understanding of strengthening mechanisms in metal alloys,” Szajewski said. “The main results relate alloy strength to collective interactions between microscopic crystalline defects known as dislocations and additional obstacle-type defects. The physical modeling conducted in these works does not rely on fitting parameters and moreover is based on an understanding of the underlying physical process. In addition, the developed physical models unify many of the results presented in earlier works found in the literature.”
The significance of this research comes down to three unique outcomes:
- The team derived a physical model that predicts material failure
- The model is novel in that it relates microscopic obstacle features such as size and shape to macroscopic material performance
- Modeling efforts by the team do not include fitting parameters and also provide unity among earlier similar research efforts
“I am optimistic that the results of this research will contribute to our scientific understanding of this strengthening mechanism in metallic alloys,” Szajewski said. “Since metallic alloys have a long–standing role in numerous engineering applications, including armor, improving our understanding of material strength may lead to improved metallic alloy development for various Soldier and vehicle applications.”
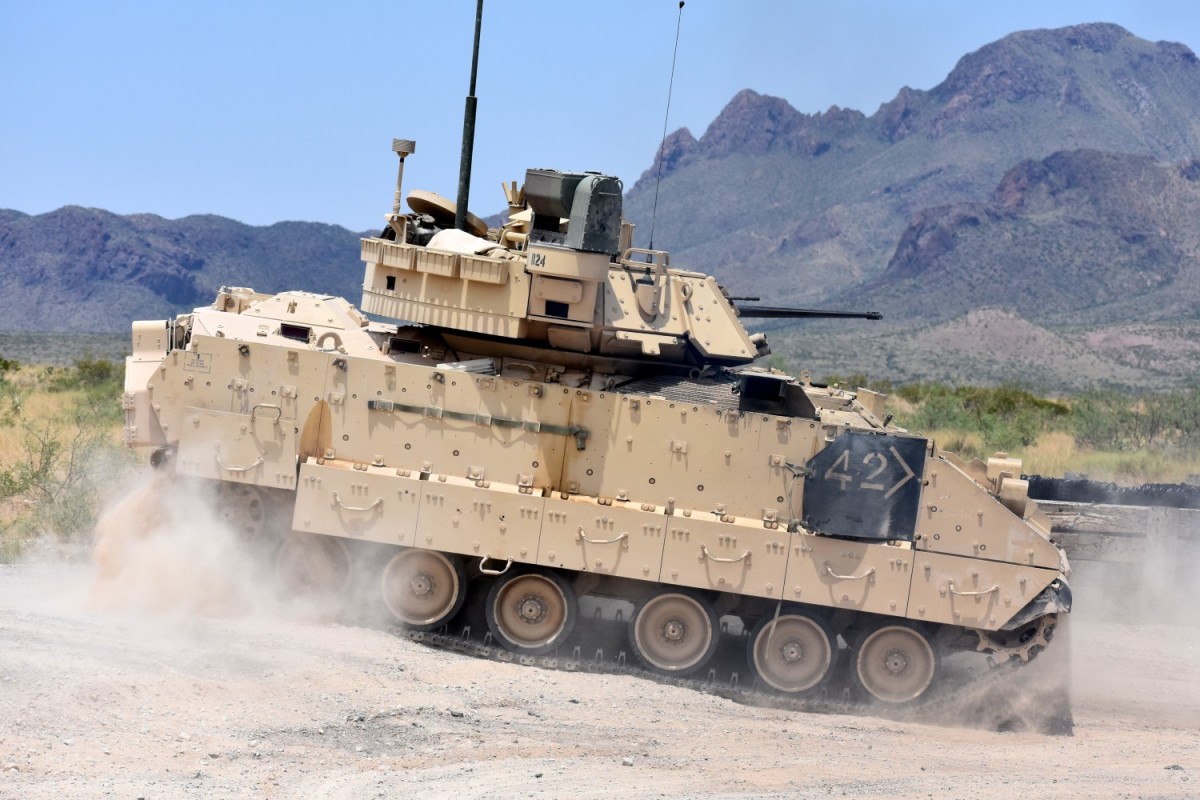
Army researchers make step toward lighter armor
Development brings potentially lighter armor with new computational and theoretical models.
