In this Viewpoint from Rolls-Royce North America, Craig McVay, senior vice president of strategic campaigns and retired Marine Corps fixed-wing aviator, discusses how the company is bringing advanced technology and support to the USAF B-52 re-engining program.
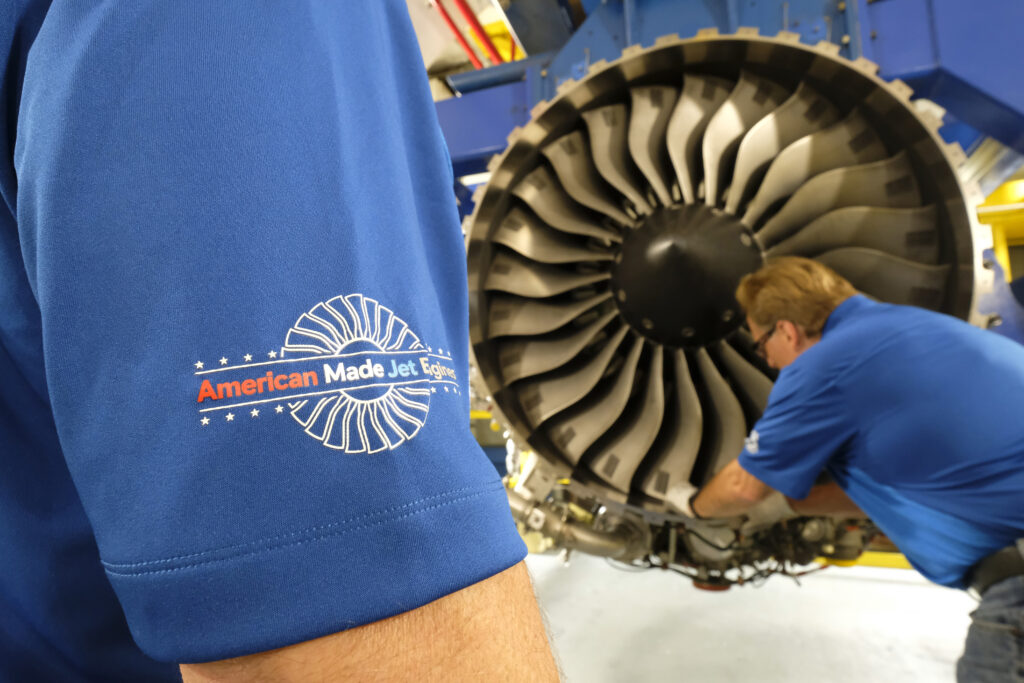
Photos of the B52 engine (F130) in the test cell at the Rolls-Royce Performance Center (Plant #5) in Indianapolis, IN, May 29, 2019. Photo by Alan Petersime
Breaking Defense: What are the specific attributes that have been incorporated into the Rolls-Royce F130 engine that help it meet the Air Force’s requirements for fuel efficiency savings and other areas for the B-52 Commercial Engine Replacement Program?
Craig McVay: We’ve spent the past couple of years carefully examining exactly what the U.S. Air Force is looking for in a modern, in-production, commercial-off-the-shelf engine for the B-52 platform, and we’re quite confident Rolls-Royce’s F130 engine is precisely what the Air Force desires. The F130 has significantly improved fuel efficiency, and offers a highly modern design that meets all of the required performance characteristics for the replacement engine. It is backed with over 27 million engine flight hours as part of the highly reliable BR700 engine family.
The F130 has been proven in both military operations and commercial service with our business aviation BR725 engine. It’s the right size, the right thrust level, and offers lower risk for integration onto the aircraft. That’s why we say the F130 is the ‘perfect fit’ for the platform. Everything about it is an ideal propulsion solution for the B-52. Additionally, we’ve already completed F130 ground testing in the test cell at our Indianapolis facilities where we will manufacture, assemble, and test the engines, should we be selected. We’ve also completed wind tunnel and digital testing. All of this helps de-risk the F130 for the B-52.
We’ve intentionally leaned forward quite aggressively to help assure the Air Force that we’re on top of our game. We’re keenly focused on measurably lowering the potential technical and schedule risk associated with integrating this engine onto the iconic B-52. Needless to say, all of this makes the F130 a highly competitive offering.
BD: Explain how Rolls-Royce will be a partner to the Air Force on the B-52 re-engining program (e.g. manufacture, support, maintenance, U.S. assembly/jobs).
McVay: First, we’ll manufacture the engines in our Rolls-Royce North America facilities in Indianapolis. These will literally be American-made jet engines should we win the competition. Our Indianapolis facilities have just completed a $600 million modernization program in equipment and technology. These advanced manufacturing facilities will be among the most modern anywhere in the industry, with efficiency improvements that will increase affordability for our F130 engines, as well as other engines we manufacture for the Air Force. Additionally, we already have a Virtual Reality training system in place for the BR725, the commercial variant of the F130, which will considerably enhance maintainability and greatly reduce cost for the Air Force’s sustainment of the F130. Overall, we’ve focused on everything possible to develop a very comprehensive and affordable solution for the Air Force when it comes to the B-52 engine selection.
BD: Improvements in digital capabilities have been a major area of interest within the Air Force. What is Rolls-Royce doing to meet these challenges, e.g. digital engineering, advanced manufacturing, aftermarket services, VR systems, etc.
McVay: Rolls-Royce has been an industry leader for years across many aspects of digital capabilities. We’ve demonstrated our strong pedigree in digital design and Model Based Systems Engineering or MBSE on the F130, as well as numerous other engines to include digital twin capabilities. We enjoy a proven track record in the area of digital test, as well as reducing risk through combining digital and test-cell capabilities to speed up the overall process.
In manufacturing, Rolls-Royce is one of the founders and leaders in the DoD-industry Manufacturing x Digital (MxD) high-tech consortium acutely focused on digital manufacturing. This puts Rolls-Royce in the forefront of the latest developments in advanced manufacturing. Rolls-Royce also uses a value-driven approach to implementing digital technologies. The aim is to reduce risk, cost, and delivery time. On the aftermarket services side, Rolls-Royce is introducing a new digital Virtual Reality maintenance training system into the Air Force for our AE 2100 engines that power the C-130J aircraft.
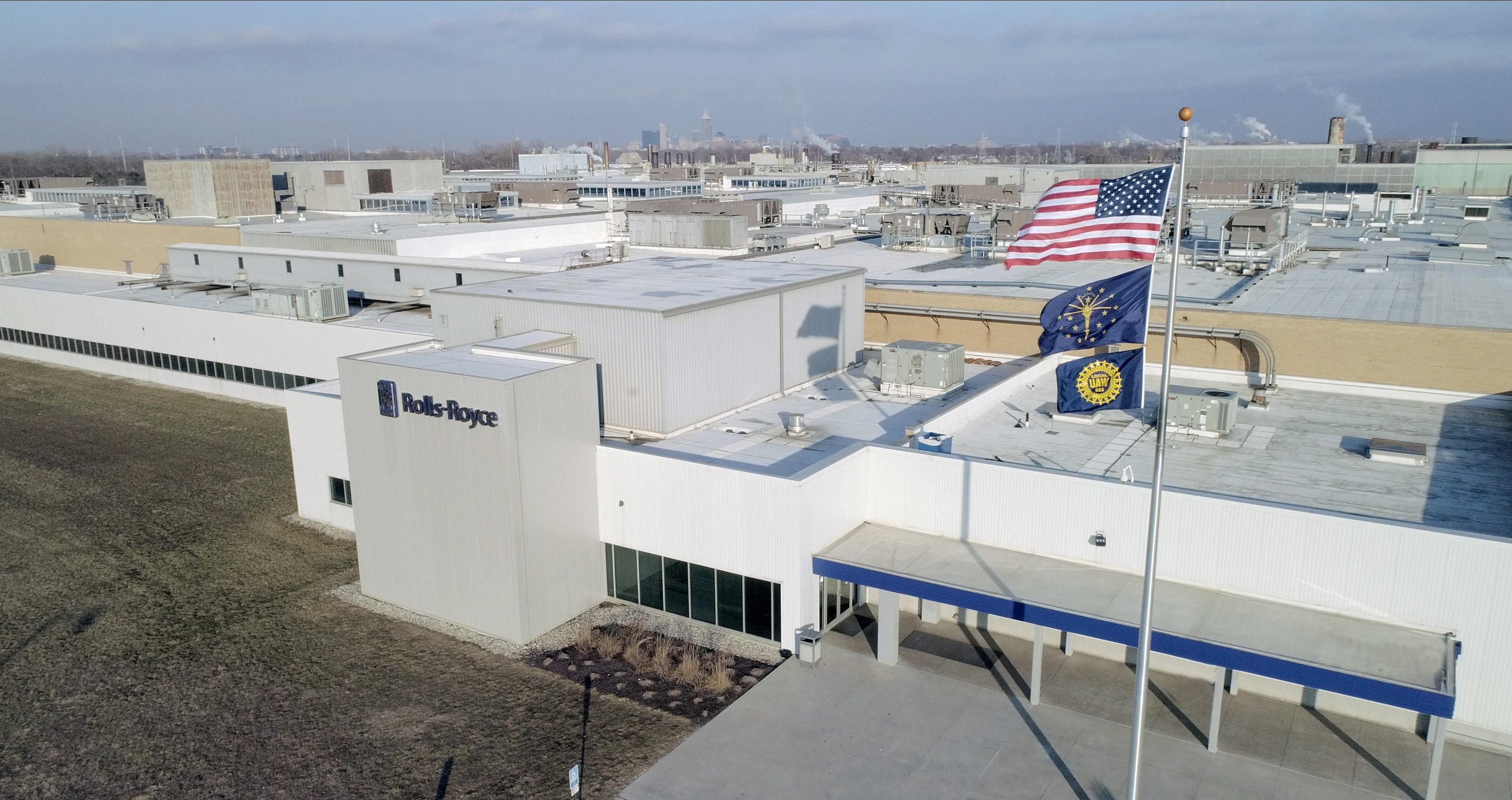
Rolls-Royce North America facilities in Indianapolis
BD: In what ways is Rolls-Royce LibertyWorks helping the DoD address the National Defense Strategy? How is LibertyWorks using agile techniques to quickly provide capabilities to the warfighter?
McVay: This year, Rolls-Royce LibertyWorks is celebrating its 25th anniversary serving the Air Force and the rest of our Defense Department customers, including DARPA, NASA, and the major airframe companies. LibertyWorks is an advanced research technology and development unit based at our Indianapolis facilities that we like to say is innovating for freedom every day. We’re certainly proud of our proven success in rapid prototyping for the Air Force. For example, we recently completed testing of a new, small, attritable engine that went from design to test in under one year, and we also successfully completed a rapid prototyping project for the Air Force AC-130W infrared suppressors, now fielded and operational.
We also have hypersonic development underway within LibertyWorks, and we’ve designed an industry leading power and thermal management system for directed energy applications, known as ColdFire. Finally, we have advanced VTOL development in the works, and have greatly expanded our digital capabilities, as I said earlier. All in all, we’re working closely with our DoD partners to understand and anticipate their needs as we develop, produce, and sustain our technology solutions in support of the warfighter. That’s what we do in LibertyWorks.
https://breakingdefense.com/2020/09...-new-engine-requirements-to-make-it-possible/