A test pilot's perspective on Qatari F-15QA trials that will pave the way to deliveries in 2021, and help the development of the USAF’s new F-15EX
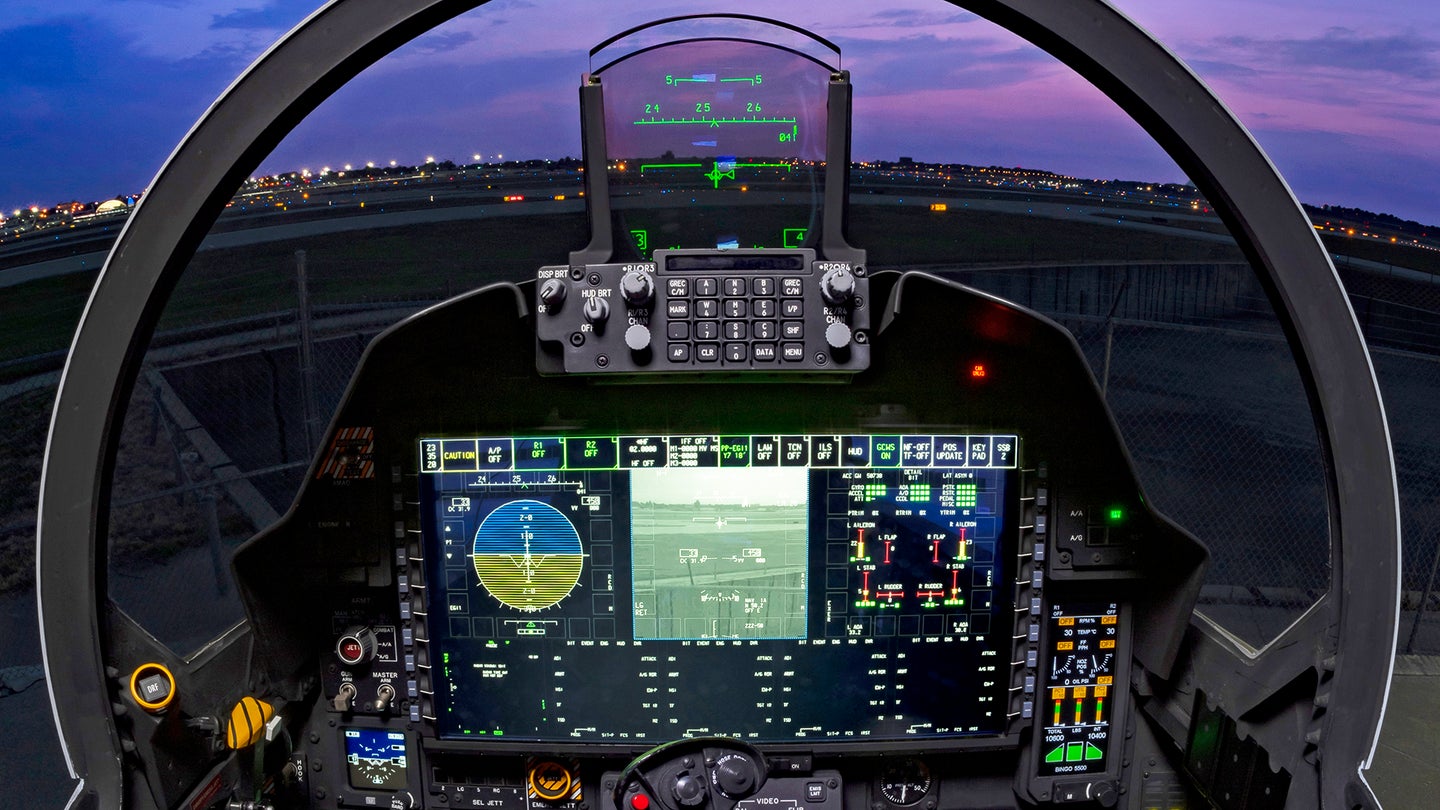
Boeing is engaged in a period of intensive flight-testing of its latest variant of the F-15, which is on order for the Qatar Emiri Air Force. The F-15QA is the most state-of-the-art variant of the Eagle to date, building upon the F-15SA that was developed for Saudi Arabia. Qatar has ordered 36 F-15QAs, which are the first to feature a new Advanced Cockpit System with Large Area Displays, among other improvements. The F-15QA is the variant upon which the U.S. Air Force’s new F-15EX will be based.
Boeing announced the first flight of the F-15QA on April 14, 2020, which took place at the manufacturer’s Lambert International Airport in St. Louis, Missouri. Three F-15QAs are currently in Boeing’s flight-test program, with two examples having been dispatched to Air Force Plant 42 at Palmdale, in California, for intensive trials in November. “This is largely a mission systems and cockpit test effort, focusing on these key areas,” explained Boeing Chief Test Pilot Matt “Phat” Giese, speaking exclusively to The War Zone.
“We are going to touch pretty much every aspect of the mission system, and make sure everything is integrated properly for this customer. This is a short part of the overall test program [for the F-15QA], and involves just a few weeks here in Palmdale. There’s some unique things we can do here from a range and airspace capability that we just can’t get at our plant in St Louis, and that’s why we have this mini deployment.”
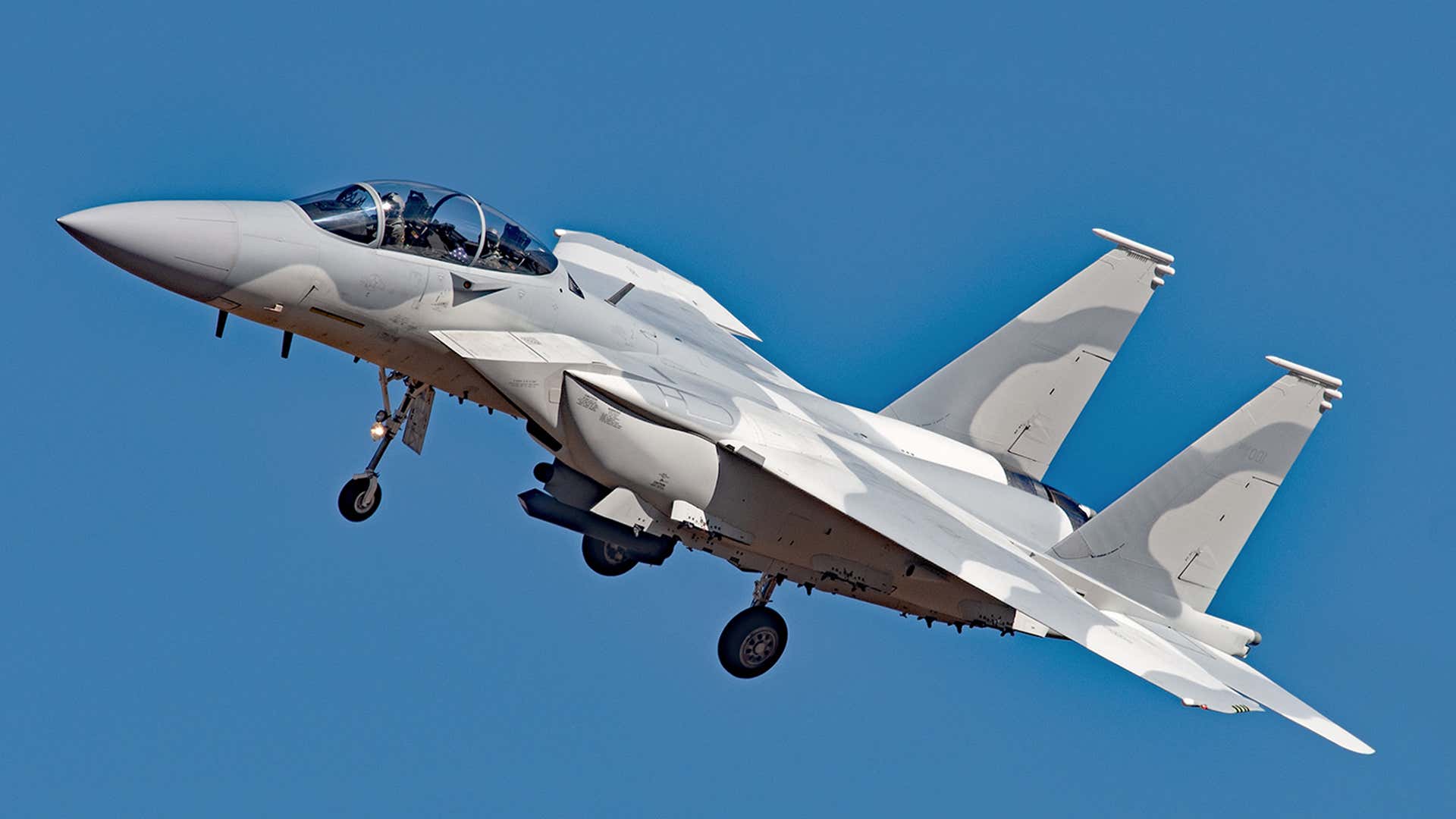
F-15QA turning final at Plant 42 in Palmdale.
Giese explained that the current test work at Palmdale is designed to ensure that the first F-15QAs are ready for delivery to the customer in 2021. “The key is to clear the critical test points that we can’t get done in St. Louis, so we can support the first ferry next year — that’s what we are driving maturity into the system for.”
“The nearby R-2508 range complex is one of the areas we are training in, so you can get the air-to-ground, low-altitude, parts completed. One of the key things out here on the west coast is the Sea Test Range for over-water testing.” Giese said that the Palmdale detachment coincided with the Boeing test team passing the 100 flight test hour milestone across the test fleet of three F-15QAs.
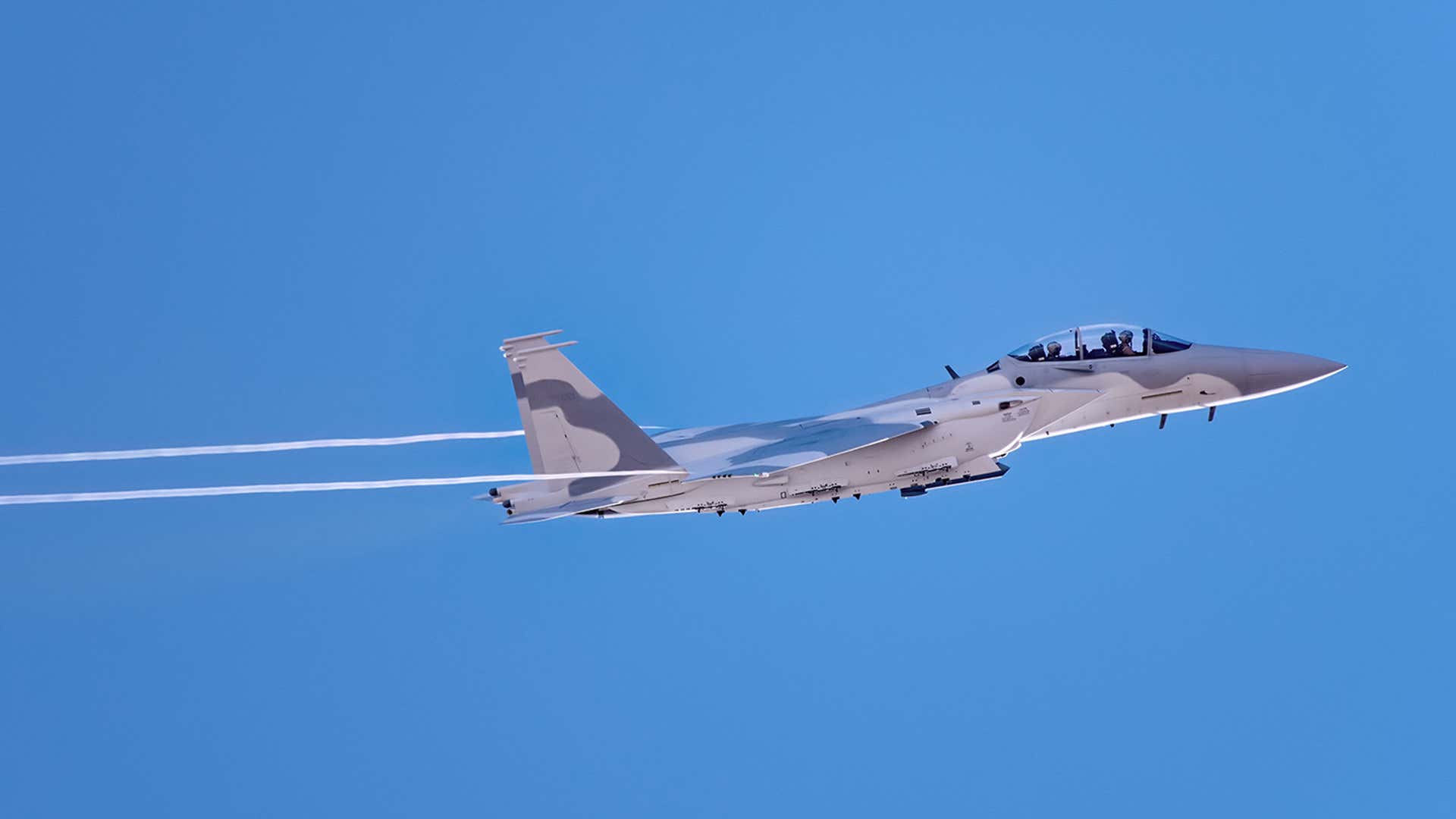
An F-15QA is put through its paces during testing at Palmdale in November.
Giese has been heavily involved in test work related to the Boeing Advanced F-15. “It was a little nostalgic bringing the F-15QA out here, as it’s been a while since we were here [testing the Royal Saudi Air Force F-15SA]. So it was exciting to get back on the site. It reminds me of the hard work we put in over a seven year period on the Advanced F-15’s digital fly-by-wire [FBW] system.” The F-15SA was the first variant of the Eagle to feature a fly-by-wire system.
“I’ve been involved from the very beginning of this new transition, where we took an incremental leap from the — for lack of a better term — “legacy” F-15 to what is now a “digital” F-15, and that happened when we made the first flight of the Saudi jet on February 20, 2013. I was a part of the subsequent testing out here, and that was full envelope — high and fast, low and slow — all the things we had to do to verify the envelope.”
The move to fly-by-wire control was a transformational leap for the F-15, and represented one of the biggest upgrades since the very first YF-15A made its maiden flight in June 1972. It meant that the Boeing test team had to effectively start from scratch when it came to evaluating the F-15SA. “The point of the flight-test program for the digital Eagle was to verify the entire flight envelope,” explains Giese. “The Advanced F-15 has new flight control computers, and a new digital architecture — so with the complete redesign we had to go out and verify numbers that had been in the tech orders since the 1970s.”
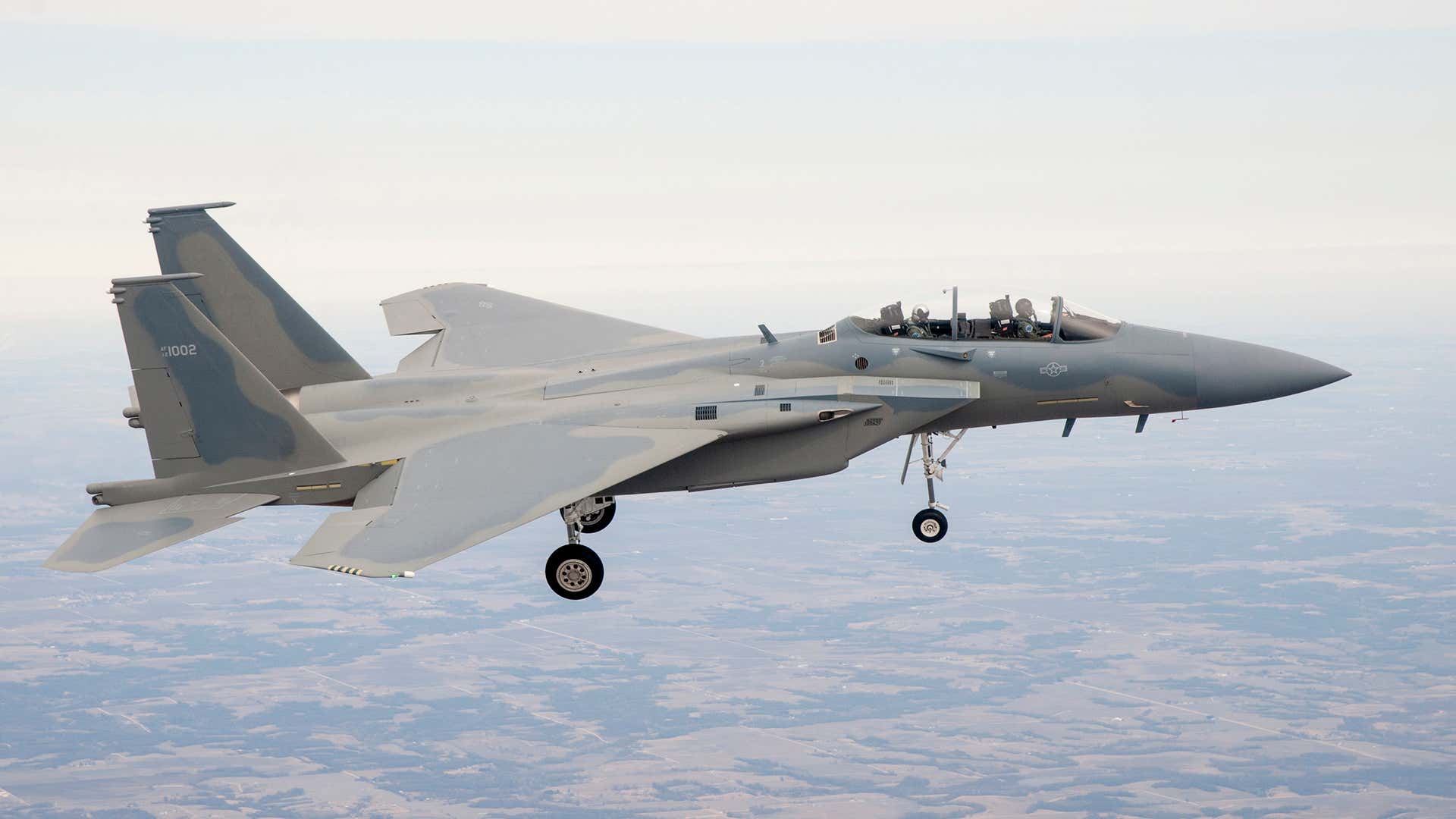
The F-15SA was the first fly-by-wire Eagle, which first flew in 2013.
“We re-validated the envelope, and verified that the performance was as good as or better — in almost all cases better — than [earlier] F-15s. Some of that testing included flutter, where you shake the airplane at very high speeds and at varying altitudes, to determine if there’s going to be any vibrations that are objectionable or cause any structural damage. We did noise and vibration testing, and high angle-of-attack work to demonstrate that the aircraft is not just a good high and fast fighter, but also able to fly slow when the pilot needs to turn hard and point at something. It was as if it was a brand new clean sheet design, and as a test pilot, I was in heaven.”
The aim of bringing fly-by-wire to the F-15 was threefold. Reliability, redundancy, and performance. “From a reliability perspective, you have two flight control computers, and each has two channels, plus quadruple inputs to each of the flight control surfaces. A quad-redundant flight control system from the flight control computers to the stabilators provides very high levels of reliability. The mean time between failures for flight control problems rose significantly higher. I can say personally, in the six-plus years of flight-test that I did on the new digital fly-by-wire flight control system, I had zero ground aborts for flight controls.”
“In the performance realm, the F-15 has always been awesome at going high and fast — we’re the only jet that gets out to Mach 2.5 — but it’s also a really good low speed, high angle-of-attack fighter if you need to get into the fight in a phonebooth with an adversary. With helmet mounted sights there’s less of a requirement to point at an adversary to prosecute an attack, but if you need to turn, the Advanced F-15 has incredible capability. Throughout the test program I tried to spin this jet, and I was unsuccessful, even with high lateral asymmetry on the platform. This is a very stable, safe, reliable, flight control system.”
The F-15QA features the same digital FBW flight control system, as well as two significant developments over the F-15SA — the new cockpit and structural enhancements. The wings and the nose barrel were completed with Boeing’s Full-Size Determinant Assembly [FSDA] production techniques. F-15 FSDA uses a process to eliminate drilling and shimming from assembly by adding fastener holes at the supplier level. This new process significantly reduces rework, increases quality, and leads to improved ergonomics. “It’s reducing parts, it’s easier to install, and it increases the life of the platform,” says Giese.
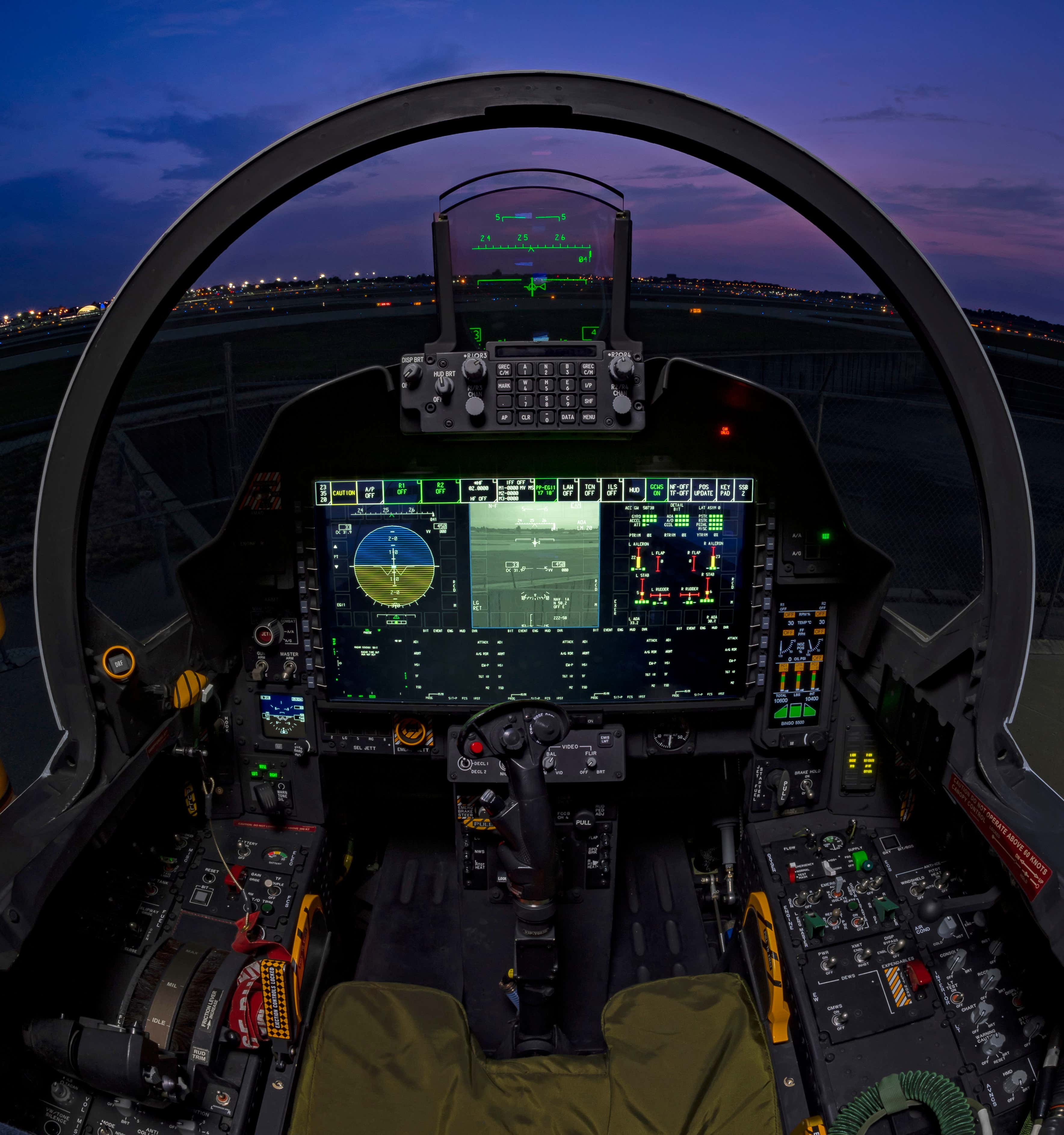
The cockpit of the Advanced F-15 complete with new Large Area Display and low-profile HUD.
“The bedrock of the new cockpit layout is the new all-glass Large Area Display [LAD],” explains Giese. “The test program for the QA is designed to mature this product.” That testing consists of verifying the major mission systems on the aircraft: such as the Raytheon AN/APG-82(v)1 Active Electronically Scanned Array (AESA) radar, and how the the LAD interfaces with what Giese calls “the heartbeat of the jet” — the ADCP II (Advanced Display Core Processor II) mission computer.
“I like to call the LAD my F-15 iPad,” smiles Giese. “It’s a 10x19-inch display that’s fitted in both cockpits, all glass, and it features an infrared [IR] touch display. Both are configurable per cockpit, so my Weapons Systems Officer can set the display in a different way to how I set up my display based on personal preference. There are a couple of different window formats that we have available and they will match the variables of the particular mission. There may be a time I’m on an eight window display, a five window display, or maybe I want two giant 9x9 windows to look at if maybe I’m doing some precise targeting. They can be changed very quickly and what we’re finding in flight-testing is that the very high-resolution color image quality of the screen allows for very precise targeting, monitoring of the sensors, and mission management.”
“We have taken a lot of lessons learned from other platforms and rolled them into this LAD technology.
You can manipulate the display with a bare or gloved finger, or move individual windows around by tapping and moving them. One of the feedbacks we got from other platforms is that in turbulent environments or if you’re under G, it can be hard to manipulate the touchscreen, so we’ve made everything on the LAD to also be controllable via the Hands-On Throttle-And-Stick [HOTAS] controls — you can move cursors, change the display format — so you don't have to actually touch the display. Other feedback we got is that some pilots just like to push a button or rotate a knob, so underneath the new low-profile Head-Up Display [HUD] is what’s called the HRCCP [HUD Radio Communications Control Panel]. This features the same digital keypad as on the LAD, so if you want to go old fashioned and hit a button or change a radio channel, you can do that — including under G or in turbulent conditions — as opposed to using the large area touch display capability. It’s the exact same format as on the LAD, so it’s not something else you have to learn.”
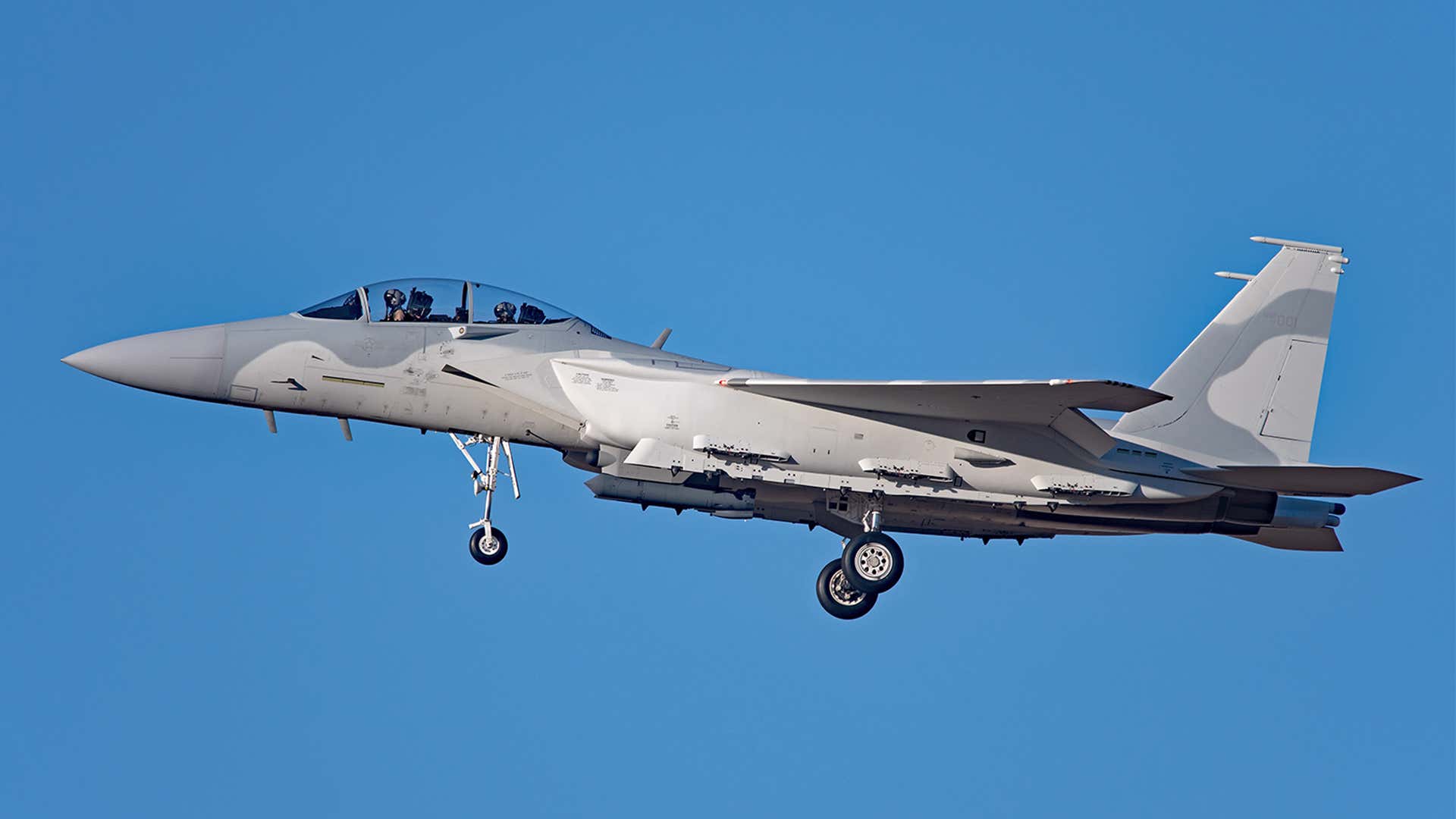
An F-15QA on approach to Palmdale in November.
The F-15QA also features the aforementioned new low profile HUD. Giese says: “It’s a little narrower than the previous HUD, more in line with the F-15C in terms of the size. We’ve learned as time moves on that the HUD is being used less and less — especially for tactical things — because we have helmet-mounted displays and the ability to keep eyes out of the cockpit and and display all of that data on a Digital Joint Helmet-Mounted Cueing System (D-JHMCS). So, reliance on the HUD is slowly diminishing. This is the baseline now, so future variants will also feature this low-profile HUD, including the F-15EX.”
A lot of the current test work, while meeting Qatari requirements, is de facto applicable to the new F-15EX for the USAF. “It’s a great effort to focus on the Qatari jets, but everything we’re doing here is going to roll into the F-15EX,” Giese endorses. “We are really going to shift our focus to delivering the F-15EX aircraft early next year for the USAF flight-test program. It’s giving us a high confidence level that this is going to be a mature delivery of those first two aircraft to the USAF early next year.”
The main difference between the F-15QA and the F-15EX is that the new USAF Eagles will include the Eagle Passive Active Warning Survivability System (EPAWSS). In addition, the F-15QA runs a bespoke customer Operational Flight Program (OFP) software, whereas the F-15EX will run OFP Suite 9, which dovetails with the current F-15E Strike Eagle and F-15C standard. It’s designed to promote commonality across the F-15 community. “I can see an operator that can quickly jump from platform to platform because of the commonality between the OFPs,” says Giese.
This was one of the key drivers for getting the F-15EX into USAF hands quickly — a ready solution that allows existing F-15C and E personnel to move seamlessly to the new jet with only minimal retraining.
Boeing intends to wrap-up F-15QA verification work in time for deliveries next year. The flight-test team will then move over to F-15EX verification testing. The work that is already being completed with the Qatari jets is helping to expedite that process, meaning that the USAF’s new Advanced F-15s will be able to meet the objective of being ready and available on the flightline in very short order — complete with all the latest bells and whistles found on the world’s most impressive Eagles to date, and more.
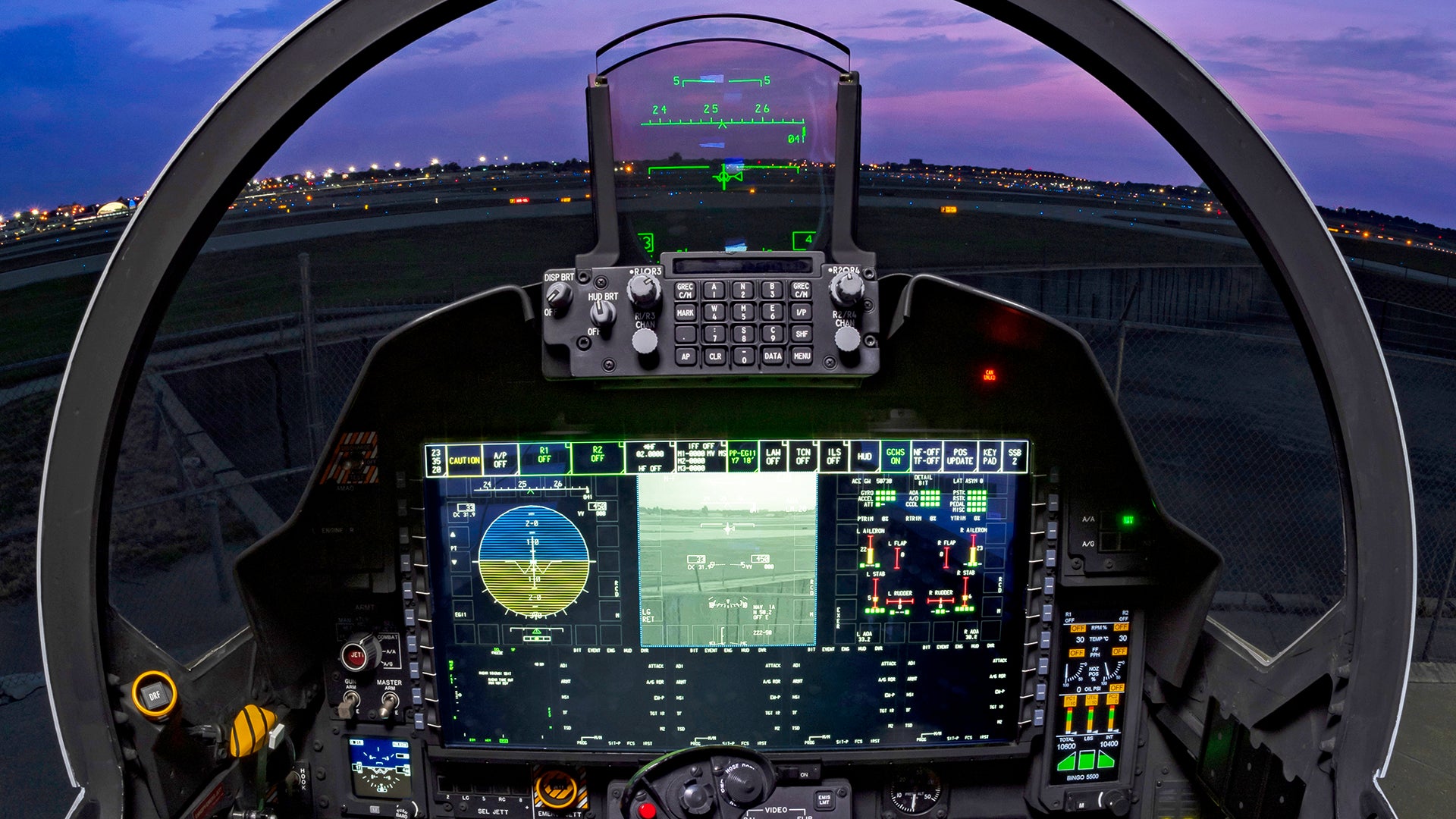
What It Is Like Flying The Most Advanced F-15 Eagle Ever Built
A test pilot's perspective on Qatari F-15QA trials that will pave the way to deliveries in 2021, and help the development of the USAF’s new F-15EX.
