GE has upgraded three test cells at its Lynn, Massachusetts facility to test the more powerful T901 rotorcraft engine (Image: GE Aviation)
GE has started ground testing the first T901-GE-900 engine, the rotorcraft engine that will power the US Army’s UH-60 Black Hawk, AH-64 Apache and Future Attack Reconnaissance Aircraft aircraft in the future.
The US Army selected the T901 to re-engine its Apache and Black Hawk fleets in 2019. The Army has also selected the 3,000-shaft horsepower T901 for the Future Attack Reconnaissance Aircraft (FARA) program.
The first engine to test milestone is being performed in a recently upgraded test cell at GE’s Lynn, Massachusetts facility. GE has upgraded three test cells in Lynn to efficiently complete the T901 engine test program.
The test cell upgrades include systems capable of absorbing the increased power and allow no-load operation of the engine, improved instrumentation capability, and upgraded test controls.
T901 engine testing will also be performed at GE’s Evendale, Ohio, facility, as well as government facilities.
Testing of the first engine is the start of a multi-year test campaign to reach full Army qualification. During the remainder of testing for the first engine, the integrated test team will perform a number of simulated flight conditions to collect performance data of the highly instrumented test engine.
“We are excited to get testing started on this engine. It is the biggest milestone to date,” said GE’s T901 program director Tom Champion. “The early testing data we’ve gathered indicates the engine is performing in line with our expectations and Army requirements.”
Compared to its predecessor, the GE T700, the T901’s 50% power increase restores aircraft performance, while its 25% better specific fuel consumption reduces fuel usage and carbon emissions. Its components are also more durable, which will lower life cycle costs.
The T901 engine also uses additive manufactured parts and ceramic matrix composites and maintains the same aircraft mounting and installation envelope as the T700.
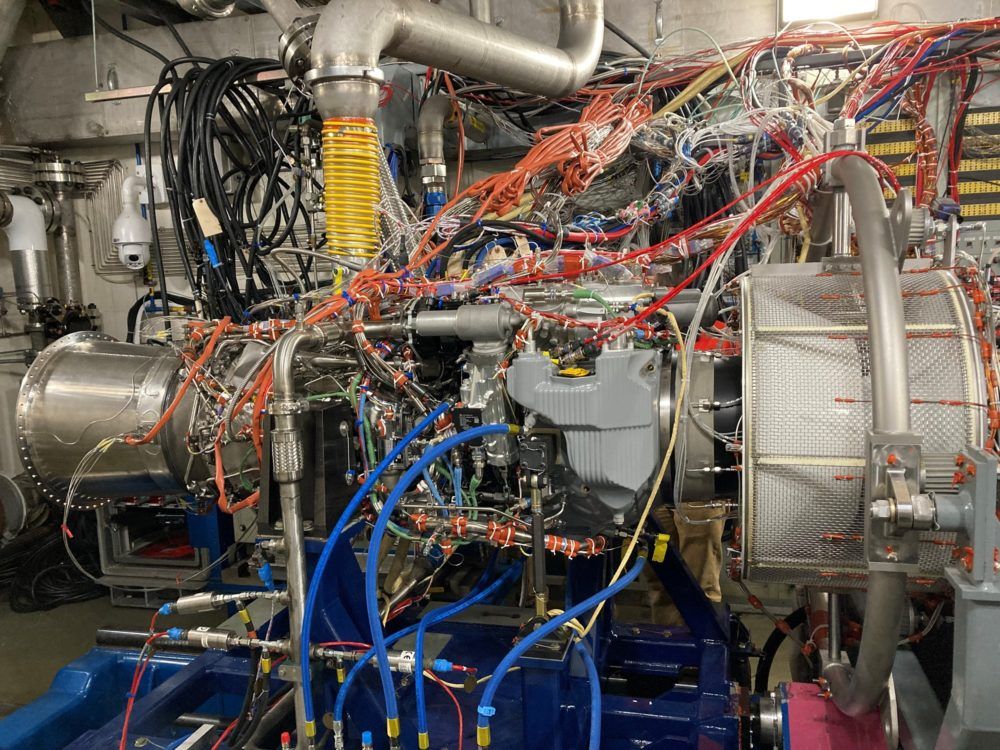
GE is testing the first T901 engine for future US Army helicopters | Aerospace Testing International
GE's T901 engine will be used to re-engine Black Hawk and Apache helicopters and in the FARA aircraft
