
Technological development observed in military engine technologies
The technological leap from piston engines to turbojet engines in military aviation history was followed by the leap from turbojet engines to turbofan engines. The next technological leap in military engine design is expected to occur with variable bypass ratio, three-flow turbofan engines. The first jet engine used in the military was the result of a top secret project that took place about 70 years ago. Unlike the past, before this new technological leap ahead, this time partners / companies are talking about it or want to talk about it.
It will be inevitable to develop new generation engines for the next generation of warplanes. Considering the ongoing studies on 6th generation platforms, it will be even more important to develop engines suitable for these platforms.
In 2007, the American Air Force, GE Aviation and Rolls-Royce consortium and Pratt & Whitney companies were selected to develop the 5th generation engine for the F-35 Joint Strike Aircraft, but after the congress decision regarding the budget cut in 2011, the joint design of GE Aviation and Rolls-Royce, F136 it was decided that the engine (while engine tests are ongoing) will not be further financed. In the following year, the most significant step in the development of the 6th generation engine was taken by the American Air Force in 2012 with the AETD program and financed both GE Aviation and Pratt & Whitney companies for engine development. There are even patents taken in 1978 for variable bypass ratio turbofan engines, which we can see as a concept for 6th generation engines. Although it has a history of 40 years as a concept / idea, platform technology also had to be developed in order to start studies in this field. The 6th generation engines are pointed out in the statements made by the British giant Rolls-Royce within the scope of the TEMPEST program, which was recently led by the UK.
In this study, I aim to explain why this concept will be needed in the future by referring to the ongoing studies for 6th generation engines with AETD and ADVENT programs and the details of the targeted engine technology and the innovations it will bring compared to 5th generation engines.
AETD Program and New Generation Engines
Before listing the advantages of 6th generation motors targeted by AETD (Adaptive Motor Technology Development) and ADVENT (Adaptive Versatile Motor Technology) programs, I aim to explain why such a change is needed by briefly touching on today's motor technology. Today (functionally functioning) turbofan engines consist of two main categories; high bypass ratio and low bypass ratio turbofan engines. High bypass rate turbofan engines are used in civil aviation due to their high efficiency and bypass rates have reached the order of> 10. Low bypass ratio turbofan engines are preferred in military platforms due to their high thrust / weight ratio.
What if we could combine these two features in a single engine and use them on military platforms? How can high performance and fuel efficiency be achieved in the same engine?

Performance vs. Yield Dilemma
We would have obtained an engine that allows to get high thrust when high thrust is needed, but to switch to a fuel-efficient mode when high thrust is not needed. Simply put, the variable bypass rate jet engine took the best of a commercial engine and combined it with the best of a combat engine to create a new architecture suitable for military platforms.

Advantages of variable bypass ratio jet engine compared to 5th generation engines
With the variable bypass rate targeted for 6th generation engines, it will be possible to switch to low fuel consumption (high bypass) mode when necessary and to high thrust (low bypass) mode when needed. As a result, it is aimed to provide ~ 25% less fuel consumption, ~ 30-35% increased range and more than 10% thrust increase compared to 5th generation engines. In order to do this, a third flow line is considered in the engine. In order to explain this issue better, it will be easier for us to look at the low bypass rate turbofan engines used today. At the fan exit, the main flow air is divided into two and some of it continues as a high pressure compressor-combustion chamber-turbines-exhaust, which we can call the core, while a part continues between the compressor body and the outer shell.

Low bypass rate jet engine (2 flow lines are seen)
In variable bypass ratio motors, on the other hand, the fan outlet air is divided into three main currents, and some of it passes through the core motor and the other two currents pass through two completely static regions. Thus, when high thrust is required, the outermost bypass part is closed and the bypass rate of the engine is reduced and the engine produces the highest thrust at the time of engagement, providing advantage to the pilot, while in other cases it aims to increase the bypass rate and provide a longer range flight.

Variable bypass rate jet engine (3 flow lines are seen)
When we compare the motors that we can call the new generation or the 6th generation with the 5th generation motors, the most important differences will be the fan module that will allow three different flows and the rotating blades made of ceramic matrix composite (CMC) material. These differences will provide a more efficient engine, higher thrust, improved heat management, increased range, and increased input recovery (inlet recovery) while reducing drag.

Variable bypass rate jet engine operating modes
In 2014, the first and only three-flow variable bypass rate turbofan engine was tested, and subsequently the preliminary design review was successfully completed in March 2015. In the first phase, the tests of the engine's preliminary design, combustion chamber, high pressure compressor and parts manufactured using CMC have been completed. In the second phase, fan tests and core engine tests were completed. Here, the highest compressor and turbine temperatures in the history of jet engines were reached. In order to achieve this progress, the importance of layered manufacturing with parts made of ceramic matrix composite (CMC) material in the engine and used in the hot zone should not be overlooked.

It is stated that the entire cost of developing the first concept engine is $ 1 billion and the cost of the entire program is approximately $ 100 billion. The version to be selected from these engines, which are being developed by GE and Pratt & Whitney, is planned to be used within the scope of the engine upgrade program to provide less fuel consumption, increased range and higher thrust in the F-35s. The image taken from Lockheed Martin's presentation that new generation motors with variable bypass ratio can be used within the scope of F-35 system development in the future is seen in the lower right corner.

Tested variable bypass ratio turbofan engine
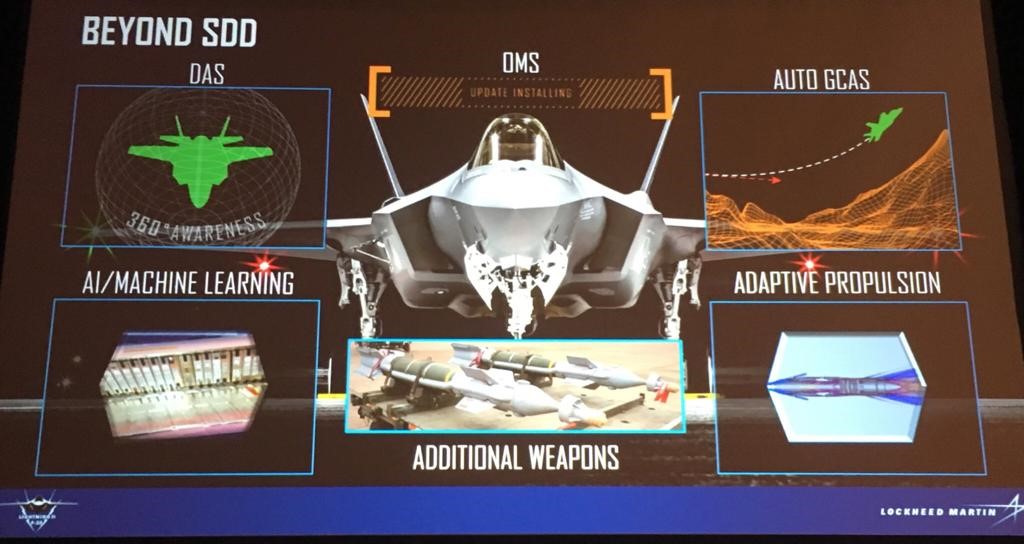
Changes considered as part of F-35 system development
Variable bypass rate turbofan engines are aimed to be designed to be used in bomber and tactical aircraft as well as attack aircraft.
TEMPEST Program and New Generation Engine Studies Started in Europe
The TEMPEST project was announced by British Defense Minister Gavin Williamson at the famous Farnborough International Air Show, also known as the Farnborough Air Show, held on July 16, 2018. As the details about the engine to be developed by the British giant Rolls-Royce in the consortium were reflected in the press, it was understood that the studies were started to develop the variable bypass ratio turbofan engine in Europe outside the American continent. The first clues were hidden in the comments by Conrad Banks, Chief Engineer for Rolls-Royce Military Engines Future Projects. Banks was talking about a motor with variable bypass ratio that would run with an integrated generator. Considering that the 6th generation platforms would be "flying power plants" (especially considering the energy need of laser guns and advanced avionics; an analogy used for 6th generation platforms), it was understood that the electrical power needed by the platform would be provided by the engine. Details about the TEMPEST program and the engine to be used began to become clear over time, which means that 1 MW electrical power is planned to be produced with the help of a generator that is planned to be integrated into the shaft of the engine.


Main Source:
- Speed and efficiency: are adaptive jet engines the way forward? – AirforceTechnology
- Pratt & Whitney
- GE Aviation
- US4080785A, “Modulating bypass variable cycle turbofan engine”, 1978
- Rolls Royce
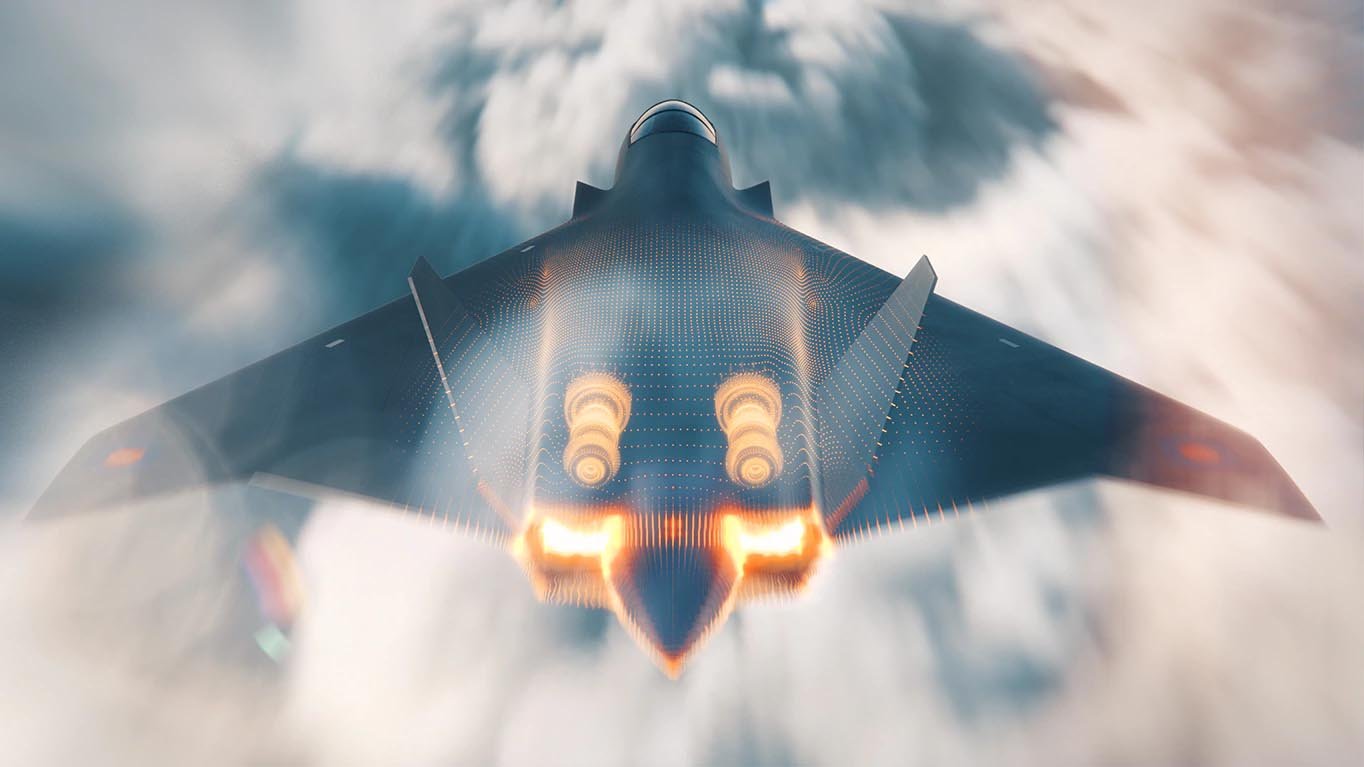
Değişken Bypass Oranlı Jet Motorları: 6. Nesil Turbofan Motorlar
Askerî havacılık tarihinde pistonlu motorlardan turbojet motorlara olan teknolojik sıçramayı, turbojet motorlardan turbofan motorlara olan sıçrama izlemiştir. Askerî amaçlı motor
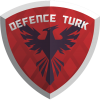