@Nilgiri @Paro @#comcom et al...
ADA Ghatak UCAV is a under-development stealth combat drone. "Ghatak" in Hindi means Lethal.
The design phase of the project has almost ended. A full scale metal version of the drone is being made for RCS measurements and optimisations. A smaller version would be made and flown powered by a Russian NPO Saturn 36MT engine to prove the control laws of the drone.
View attachment 2709
View attachment 2702
The full scale version would be powered by a dry version of the GTRE GTX-35VS Kaveri engine. Dry version as in without the afterburner. The Kaveri produces 52KN of thrust at a power to weight ratio of 7.8:1. Enough for a combat drone :
View attachment 2710
View attachment 2711
Note the nozzle section, as shown here are just an interim thing. These photos are from AeroIndia 2015 and the Ghatak project was in very early stages then. The UAV was aimed at being stealthy so its likely that it might end up with a more stealthier nozzle design.
The Kaveri project was handed over to the GTRE because they were the only organisation in the country with experience in turbines at that time. GTRE had developed the GTX37-14U afterburning turbojet engine. So the work for them appeared simple at the first glance. All they had to do was to cover up the turbojet with a turbine tube and attach a compressor fan at the front. This would create a bypass flow around the core, thus turning the engine to a turbofan. Simple right ? The problem arrived when the fan was attached and the turbine inlet temperature increased rapidly often melting internals. Our materials technology couldn't keep up with this. So a small bypass ratio of 0.16:1 adopted. At this small a bypass ratio, the Kaveri is more of a "leaky turbojet" than a true turbofan.
Extensive modifications were done to the GTX37-14U turbojet . Eventually the new turbojet was named "Kabini". The Kabini serves as the core of the Kaveri engine. Here is an old photo of the core :
View attachment 2703
Getting back to the UCAV. Since it is a stealth UCAV it has a compact serpentine intake duct to hide the engine from radar waves. This kind of an intake tube will create large distortions of air pressure at the fan of the engine. This increases the chances of compressor stalling.
View attachment 2708
The problem of distortions are to be countered in 2 ways. One is by introducing vortex generators into the serpentine intake duct to somewhat stabilise the air flow fluctuations & the other is by designing a new compressor fan which is more tolerant of inlet distortions. The new fan design was shown in AeroIndia 2019
View attachment 2706
Fabrication work of the fan has been completed. We are currently testing the engine performance when it is mated to the serpentine duct.
Fan components :
3D printed anti-icing assembly on the variable inlet guide vanes & front bearing of the drive shaft assembly for the Kaveri jet engine :
View attachment 2698
View attachment 2701
View attachment 2700
Look at those long chord blades. Beautiful.
Our grasp of metallurgy/coatings etc have gotten a lot better since the 1980s. We did test a scramjet recently, the temp faced by that engine is much greater.
For the Kaveri GTRE has developed single crystal blades & vanes, Yttria-stabilised cubic zirconia thermal barrier coatings. These two combined should give us over 1800 K turbine inlet temperature capability, currently its at 1700 K. That would also allow us to increase bypass ratio & over-all pressure ratio which would further give us more power, better efficiency & better thrust to weigh ratio.
All of this is great but we need to be able to manufacture these things at least in quantity. Thankfully there has been some movement on that front. Recently GTRE has invited "reputed Indian Industries/Orgs" with minimum 2 years experience of aerospace-grade manufacturing for component manufacturing, module-level assembly, engine level integration & delivery to GTRE of 50kN class aero-engine.
- The plan is to make 5 engines in first 3-4 years, to be made with GTRE as Lead System Integrator(LSI).
- 15 more engines over the next 3-4 years with an industry partner taking over LSI role.
- Sum total of only 20 engines over next 7-8 years.
- A production run of 70-80 engines is envisaged thereafter over 10-12 years.
- The first 5 engines planned to be realized at a 3-month interval with subsequent engines made at 2-month intervals.
HAL is an obvious player. Others like Bharat Forge, TATA Aerospace Systems Ltd., L&T Aerospace, Godrej & Boyce Aerospace are all likely to go for it. If they are planning a production run of 80 engines then we will probably order 40 of the Ghatak UCAVs, assuming each uses up 2 engines in its lifetime. Would've preferred a larger order, but with the budgetary constraints 40 is not bad.
So SWiFT took its first flight. CLAWS validation flights have commenced a bit late. It was scheduled for August 2020. COVID might be the reason. @Nilgiri @Paro @Zapper et al you guys seen this ?
ADA-IISc's remotely piloted aircraft successfully test flown
By Hemanth CS
Updated: Nov 3, 2020, 06:00 IST
The maiden test flight was carried out at TAAL airfield in Hosur
A prototype of a delta wing remotely piloted aircraft designed and developed by the Aeronautical Development Agency (ADA) and the Indian Institute of the Science (IISc) was recently successfully test flown.
This prototype of a delta wing remotely piloted aircraft or unmanned aerial vehicle (UAV) with Micro Jet Engine Propulsion is said to be the first-of-its-kind developed and flight tested in the country. Terming this a defence project, an official said that the project is a joint collaboration between the ADA and the IISc’s Department of Aerospace Engineering.
“This is a defence project where the design for the prototype has come from the ADA, while the mould composition, integration of the airframes, engine, fuel tank along with the testing was done by the Department of Aerospace Engineering’s UAV lab which has a lot of expertise in the developing these kind of aircraft,” an official told BM.
The ADA which is the nodal agency for LCA Tejas is also involved in the design and development of the Autonomous Unmanned Research Aircraft (AURA).
The official refused to comment on whether the delta wing remotely piloted aircraft is being developed to carry weapon payloads.
The maiden test flight of the prototype was carried out at the Taneja Aerospace and Aviation Ltd (TAAL) airfield in Hosur. Further giving out details about the flight parameters of the maiden flight, the official said that the aircraft attained a maximum velocity of 190 kmph per hour at 50 per cent throttle, while the take off velocity was 155 kmph and approach velocity was 130 kmph.
“Since this was the first flight we did not want to take much risk with the speed and flew only with 50 per cent throttle. This aircraft is designed for higher speed it can attain a velocity upto 300 kmph,” he said.
KingTech-140 Turbine
During the flight, the aircraft which is powered by Kingtech 140 attained an altitude of 100 metres.
“ To the best of our knowledge, this is the first-of-its-kind indigenous project to be successfully developed and tested in the country. Over the world there are plenty of such aircraft with delta wing configuration especially flown by forces of US and Israel,” the official added.
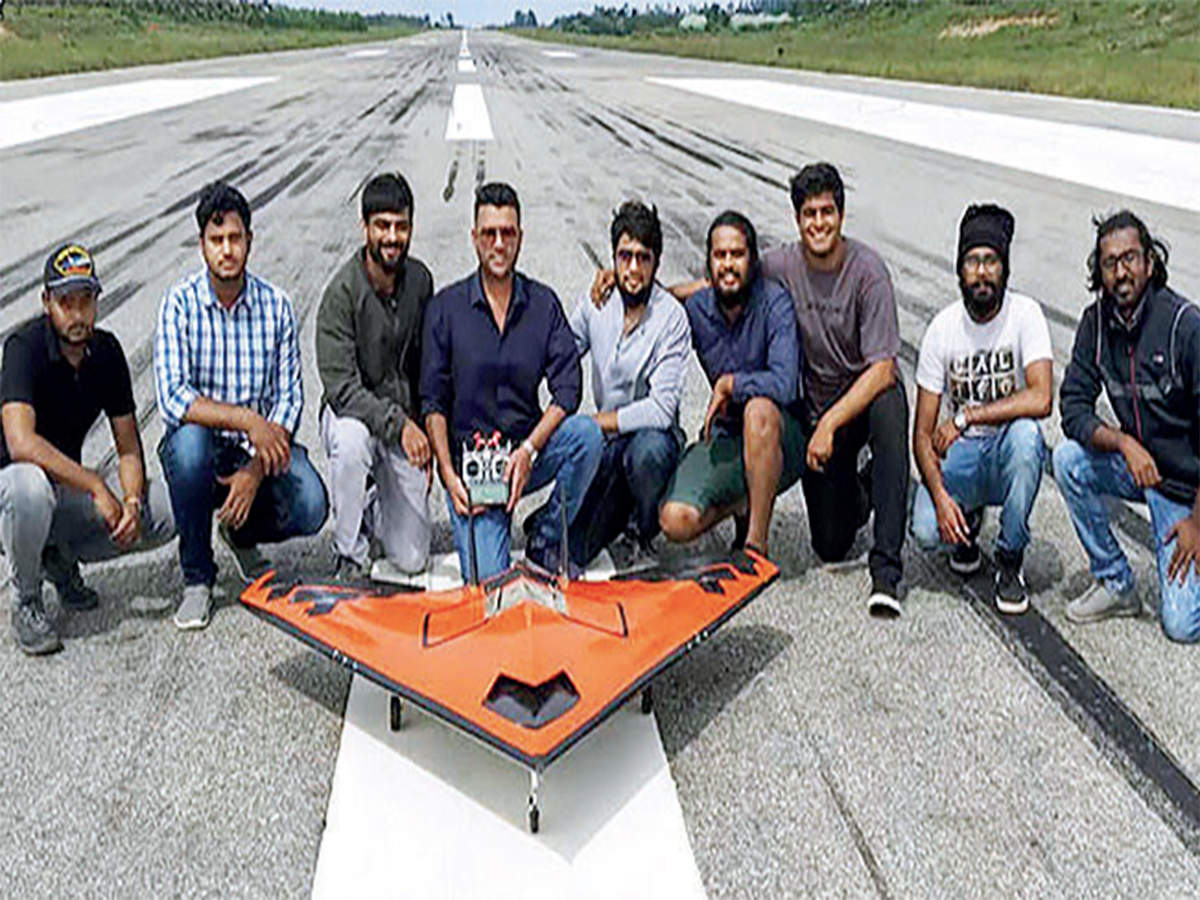
ADA-IISc's remotely piloted aircraft successfully test flown
This prototype of a delta wing remotely piloted aircraft or unmanned aerial vehicle (UAV) with Micro Jet Engine Propulsion is said to be the first-of-its-kind developed and flight tested in the country.